3D Core Wild Style
Linkage optimization for DMLS
Alvaro Dal Farra, professional athlete, entrepreneur and author of many initiatives, is a leading figure in the world of additive manufacturing. In 2019, in collaboration with Codoro Studio and PUNTOZERO, he revolutionized the concept of motorbike customization through 3D printing. The result? The Kawasaki Kx 450 3D Core, a one-of-a-kind masterpiece.
After the initial triumph, Alvaro continued on the path of innovation, implementing a fundamental evolutionary upgrade. He introduced a new structural part: the suspension linkages, made with innovative metal alloys through Additive Manufacturing technology.
Project objectives
- Weight reduction
- Improved mechanical stiffness
- Aesthetic improvement
- Use of innovative technology
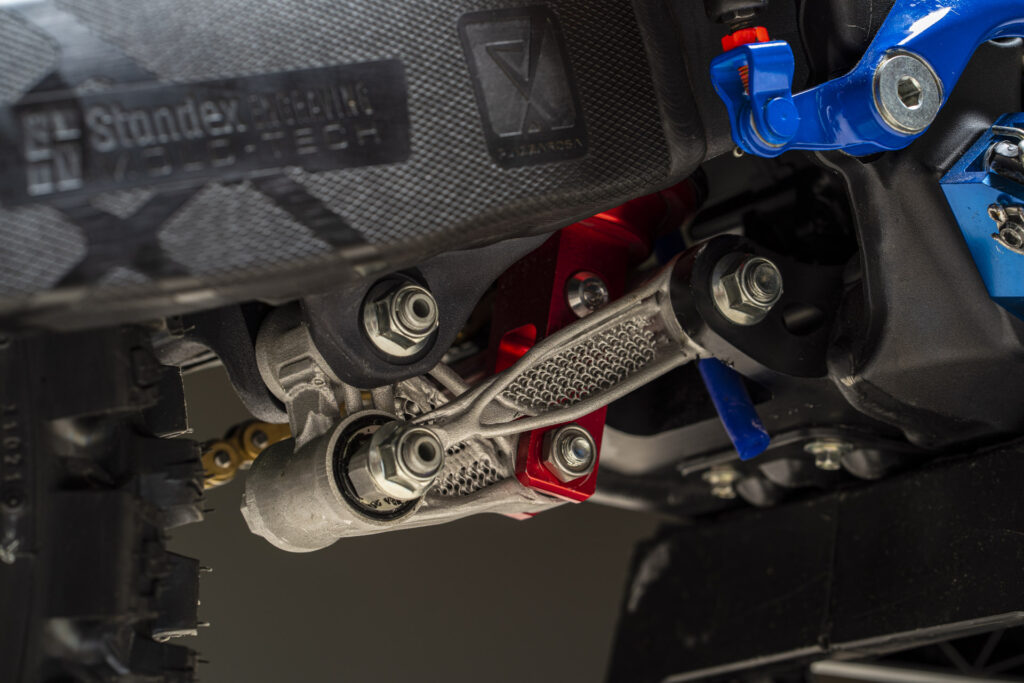
pROBLEM
More than a problem in this case we started from a challenge, namely that of improving a structural component of a motocross bike thanks to an innovative design and the use of additive technologies.
Therefore, starting from an analysis of the original component we tried to optimize the component from an additive perspective.
SOLUtion
Using ntopology and Inspire we created a component that is first and foremost lighter than the original one.
Furthermore, wanting to optimize performance, we increased the mechanical rigidity in order to improve the performance of the component and consequently of the entire two-wheeled vehicle.
development
We started from the increase in design space, however
We have therefore replaced the metal with plastic without affecting the performance of the component.
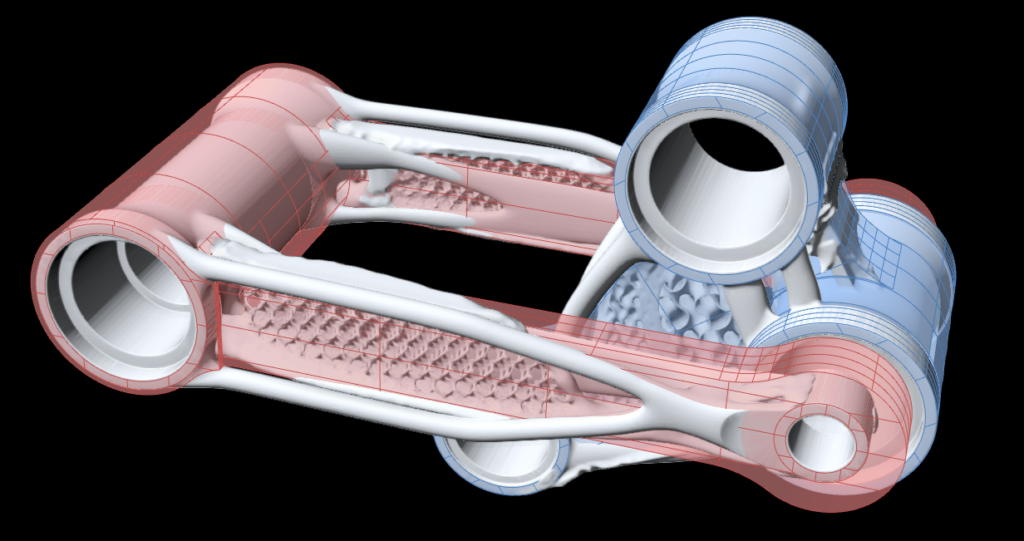
Intro
The redesign of the linkages embraced the concept of optimization inspired by nature, using complex shapes to achieve extreme weight reduction and a significant increase in rigidity.
The chosen style and the color combinations recall the “Wild Style” era, when the street dictated fashion, accompanied by rap music and graffiti. The story of Alvaro Dal Farra is an ode to innovation, aesthetics and the harmonious fusion between technology and passion for the unique design of his motorcycles.
However, technology alone is not enough, to achieve concrete advantages it is also necessary to redesign the components to make them suitable for Additive production.
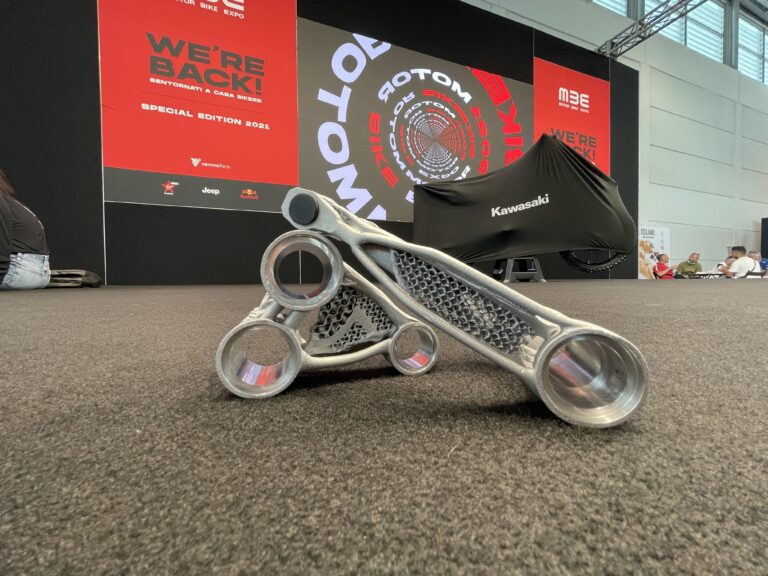
The project
The leverage has been redesigned taking inspiration from the concept of optimization of nature, achieving 2 goals through complex shapes:
- Extreme weight reduction
- Increased stiffness
Development
Starting from a structural analysis of the forces that the leverage system must withstand using the Solidthinking Inspire software, it was possible to carry out a dynamic study based on the different contexts. To optimize solution times and reduce the number of parts, the model has been simplified.
The swingarm and linkages were connected to the frame via rotating joints. The front shock absorbing system has been simplified by considering a single fork rigidly connected to the steering head. The engine was considered as a mass rigidly connected to the chassis. To optimize solution times and reduce the number of parts, the model has been simplified.
The swingarm and linkages were connected to the frame via rotating joints. The front shock absorbing system has been simplified by considering a single fork rigidly connected to the steering head. The engine was considered as a mass rigidly connected to the chassis.
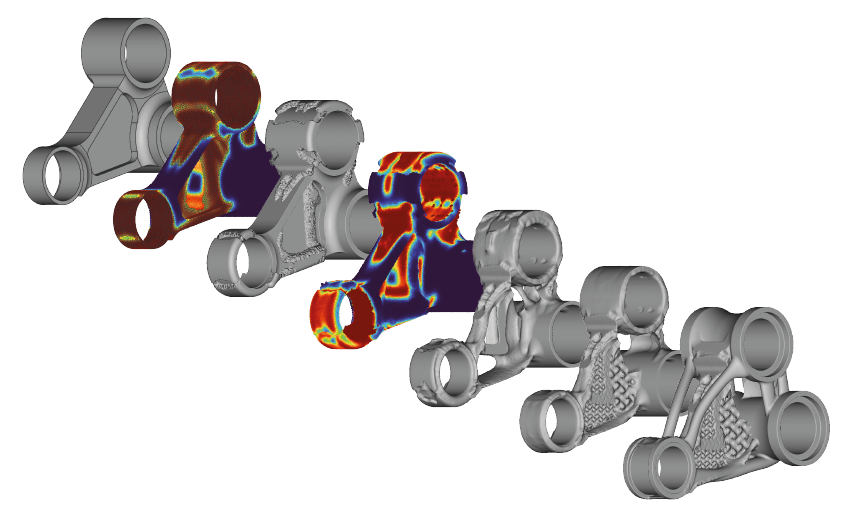
The first optimization was done starting from the original design space with the aim of minimizing the mass. The optimized component was created using DMLS technology with an innovative aluminum alloy m4p™ StrengthAl, a material characterized by the highest obtainable yield strength, which reaches values almost double compared to the AlSi10Mg alloy, making it particularly suitable for high-performance applications in the automotive and aerospace.
To further increase the stiffness it was decided to go beyond the limits of the initial design space, to have lines of force inside the component with a trend that does not depend on the starting design space.
Form = Function
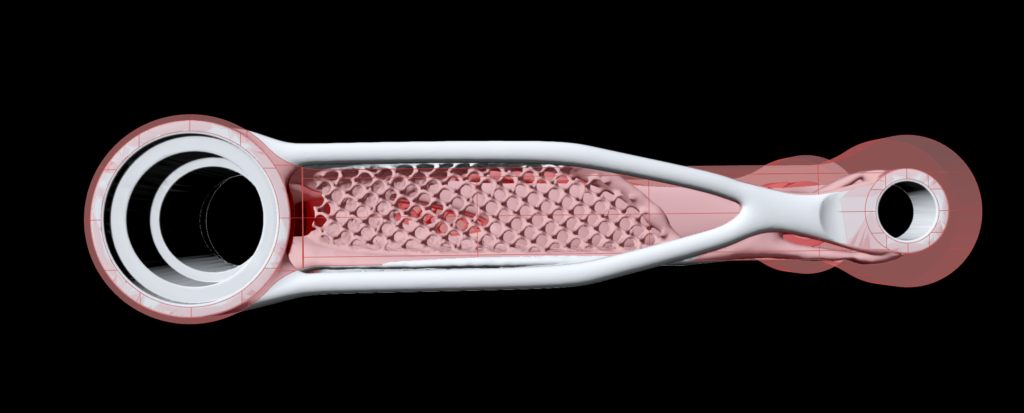
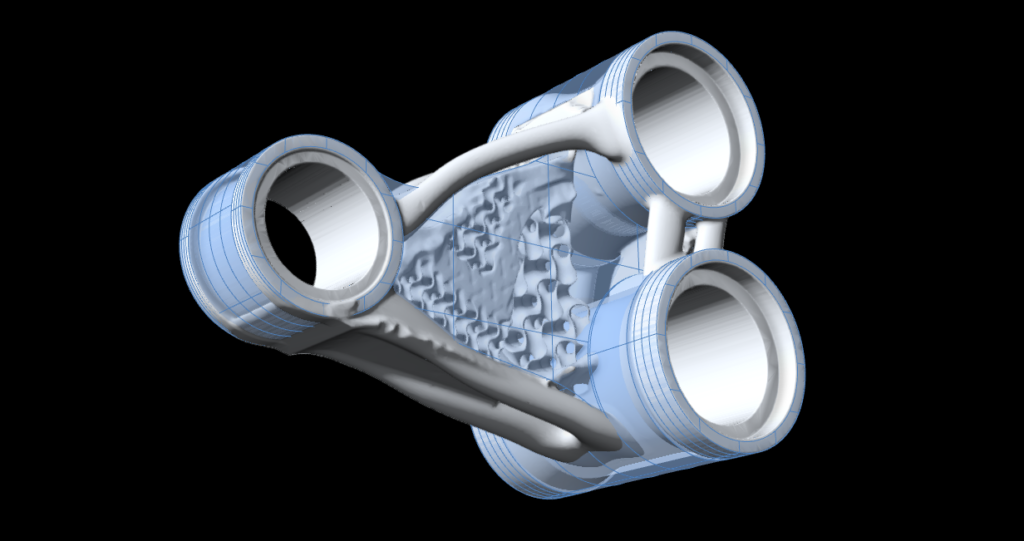
The 3D Core Wild Style maintains the “standard” line of the 2021 KX but thanks to the new processes the bike is more complete; research into details enhances the new characteristics of this vehicle
– Technology: Additive Manufacturing – DMLS + an innovative aluminum alloy designed for the aerospace and motorsport sectors
– Design: ALTAIR and nTopology
– Engineering: Structural and improvement engineering study
– Design: innovation of line and style
Materials and technologies, shapes and geometries are closely related in all types of design, but in DfAM an appropriate combination can lead to significantly innovative results. Based on the structures that we are asked to develop, we can endow the material with particular properties: for example, we can create very dense latex structures to stiffen a soft material or, vice versa, reduced density latex structures to make a material almost flexible rigid by nature.
The project in numbers
Time reduction
2/3 weeks
vs
1 week
Weight reduction
- 62%
Cost reduction
384€ cad
vs
88€ cad
Stress reduction
- 38%