3D ski goggles
Product innovation
This ski goggle was designed using the power of computational design, an approach to design that uses calculation and computer science principles to generate complex shapes and geometries aimed at optimizing components and finished products. We have brought innovation to a sector still very tied to very traditional technologies and materials.
Project objectives
- Maximizing comfort
- Breathability
- Exclusive design
- Waterproof
- Customization
- Reduction of production and assembly times
- Use of innovative materials and technologies
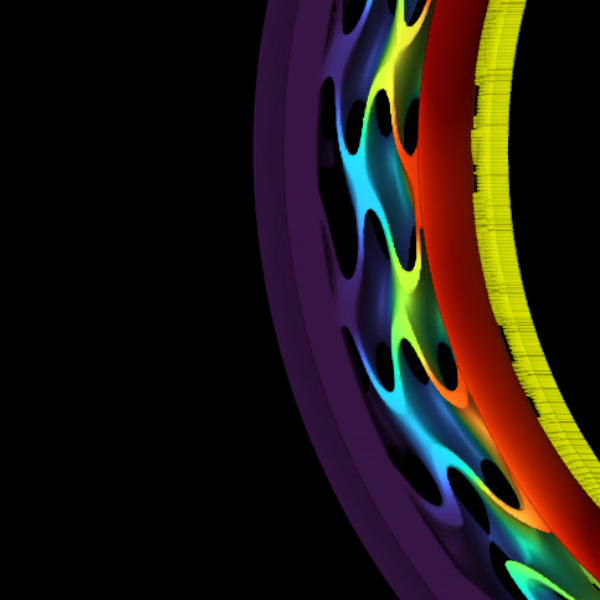
pROBLEM
The world of ski goggles is characterized by strong innovation on the lenses while at the level of the supporting structure this is created using injection molds and foam rubber. This creates problems related to the need to produce large quantities at the expense of customization. Furthermore, these traditional materials do not allow air to escape, thus causing the lens to fog up.
SOLUTION
Thanks to an accurate feasibility study and a series of iterations we have developed a frame composed of a single 3D printed piece that is completely customizable, comfortable, breathable and waterproof.
HP’s MJF technology also proved to be ideal in this project both in terms of printing times and technical feasibility.
DEVELOPMENT
To ensure maximum comfort in contact with the face and good rigidity for lens assembly, a gradient latex structure was developed.
To promote breathability, an external skin that is waterproof but breathable at the same time has been developed, for adequate air circulation.
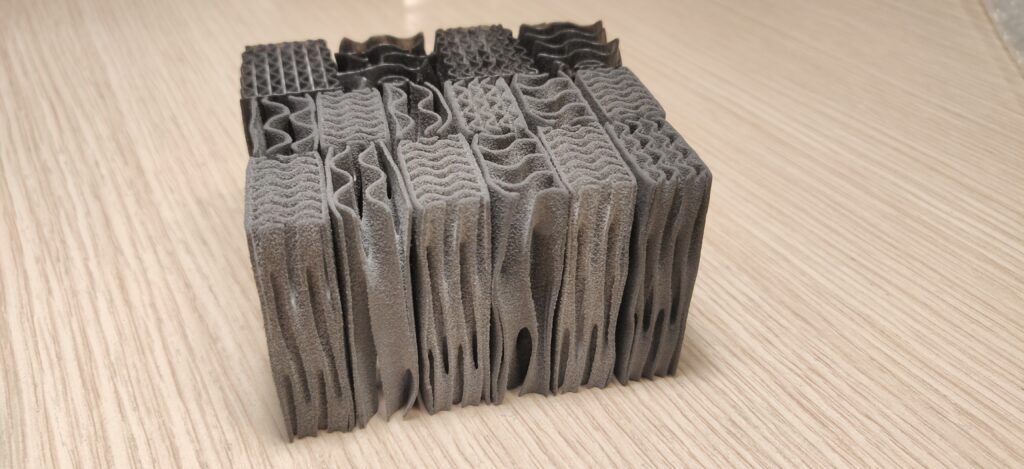
Intro
We developed this project thinking about how to innovate the world of masks thanks to the use of additive manufacturing.
Bringing innovation only makes sense if there is a simultaneous improvement of the product, which is why our objective in this project was not only the use of 3D printing but above all the improvement of the product itself.
Creating a unique component by eliminating not only equipment costs (a typical advantage of 3D printing) but also assembly costs has allowed us to bring innovation not only to the product but also to the process.
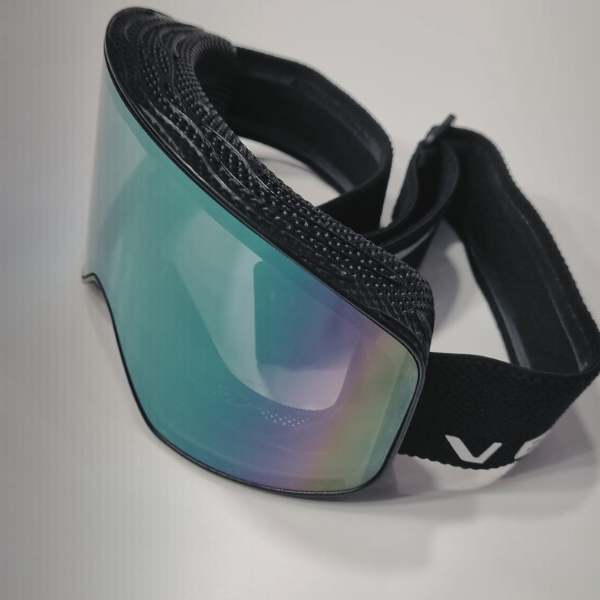
The project
The customer asked us to develop a ski goggle with clear project objectives, to bring innovation to the goggle sector and resolve traditional problems related to equipment costs, especially in the case of limited series.
Development
The external skin was designed taking inspiration from the lotus leaf which, thanks to its microstructure, gives the plant water-repellent properties.
This structure allowed us to create a component that blocks the passage of water but at the same time guarantees an excellent level of breathability.
The TPMS (Triply Periodic Minimal Surface) structure follows the curvature of the mask, so as to have the same behavior along the entire support profile of the face.
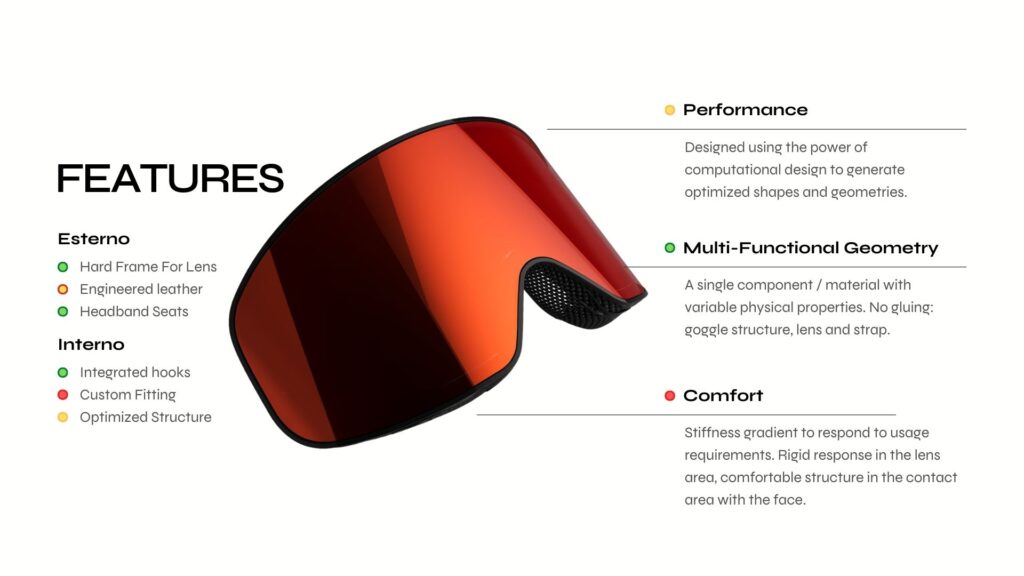
Innovate, Improve, Solve
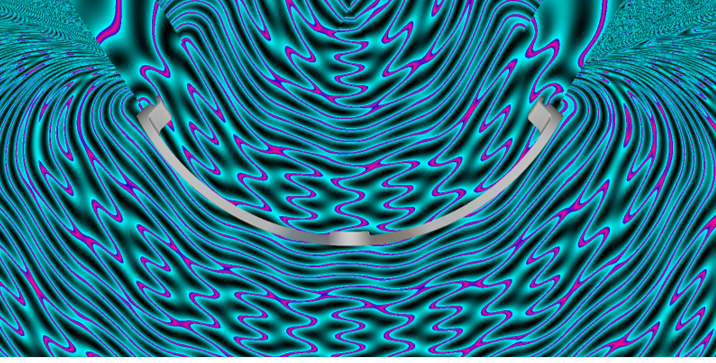
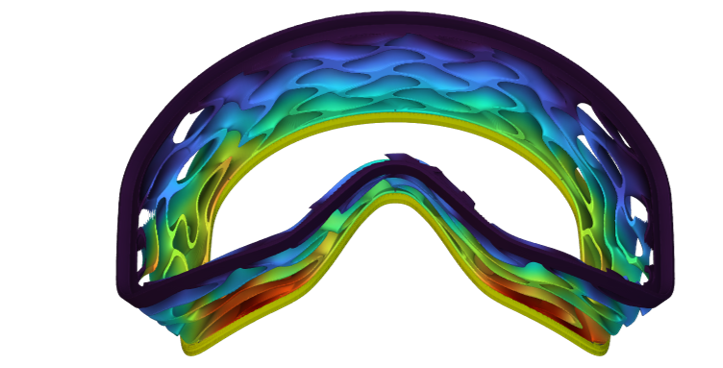
MJF HP technology perfectly matches all the needs of this project.
The BASF TPU material used gave the right balance between flexibility and rigidity of the component, furthermore, being biocompatible, it is ideal for contact with the skin.
Going through a series of geometries and samples we developed a project that met the customer’s objectives and was 3D printable at a sustainable cost. Working on these 2 fronts, we have developed in close collaboration with Nomec an innovative solution, currently patent pending, printing the Basf TPU structure with HP’s MultiJet Fusion technology.
Il progetto in numeri
Riduzione tempo
2/3 settimane
vs
1 settimana
Riduzione componenti da assemblare
3 vs 5
Riduzione costi
eliminazione dei costi di attrezzature
Traspirabilità
passaggio dell'aria garantito