Design revolution
3D printed orthopedic prosthesis
A working team of very young experts in Design for Additive Manufacturing – Francesco Leonardi and Ivan Vecchio (@PUNTOZERO) and Gianluigi Rossi (@ADD+it) – starting from the idea and analyzing with utmost care the state of the art on prosthesis projects orthopedics in 3D printing has designed an innovative solution: sustainable, scalable and repeatable but above all to satisfy the patient’s requests.
This project was born from a real case study, from a need of a patient who has not yet found the ideal prosthetic solution for his lifestyle.
sostenibile, scalabile e ripetibile ma che soprattutto andasse a soddisfare le richieste del paziente.
Questo progetto nasce da un caso di studio reale, da un’esigenza di un paziente che non ha ancora trovato la soluzione protesica ideale per il suo stile di vita.
Project objectives
- Maximizing comfort
- Breathability
- Lightening
- Interchangeability
- Maximizing Customization
- Reduction of production times
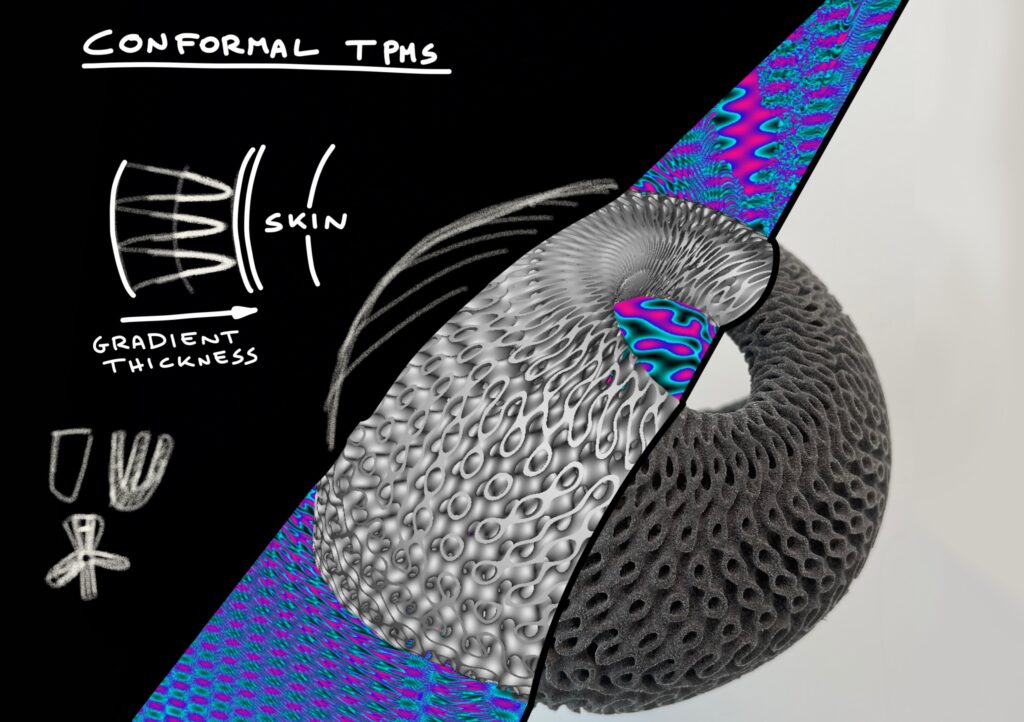
PROBLEM
The project was developed on a specific patient. The patient’s requests were the possibility of having a comfortable prosthesis, which allowed breathability and was lighter than traditional prostheses. Furthermore, the patient needed to modify the prosthesis in relation to the change in temperature but also based on the type of activity performed. (sports, walking, etc.)
SOLUTION
The combination of additive technologies with specific design techniques led us to an extraordinary result.
We have in fact created a structure that maximizes the supply of air and, at the same time, minimizes direct contact with the leg in order to eliminate the thick silicone sock necessary for the vacuum.
DEVELOPMENT
To give the right rigidity to the external part of the product and the softness required for the internal part, we created an architected material based on the gyroidal TPMS structure, to guarantee more precise control both on compliance and on variable thicknesses.
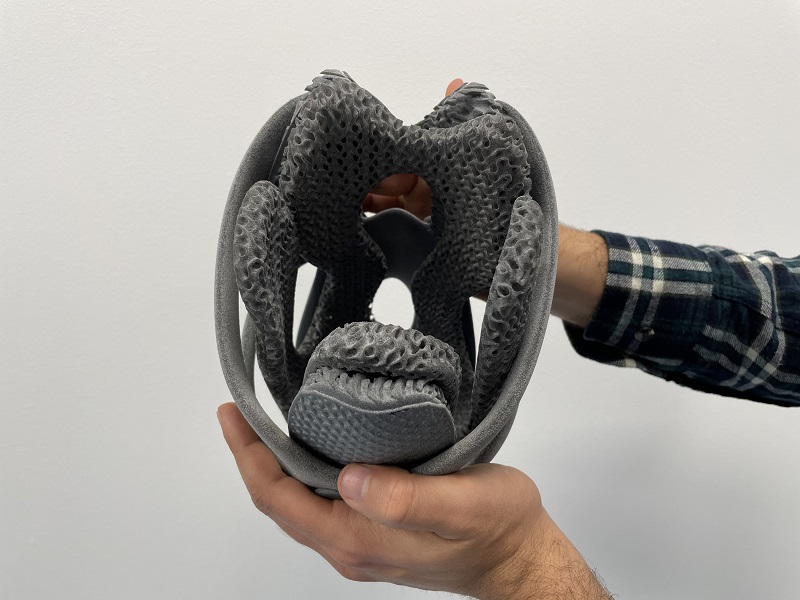
Intro
Today the task of doctors, engineers and many other categories of professionals is to make our lives better, and this is precisely the main objective of the project: to make our engineering knowledge available to improve the lives of those who, for example, every day he has to wear a prosthesis to be able to carry out normal routine activities and more.
We strongly believe that a specific combination of shape and materials, together with a specific suspension system, determines the good design for more comfortable and breathable dentures. During the development phases of our project, we took all these interconnected parameters into account and overcame the old labor-intensive and time-consuming mold design process with Additive Manufacturing.
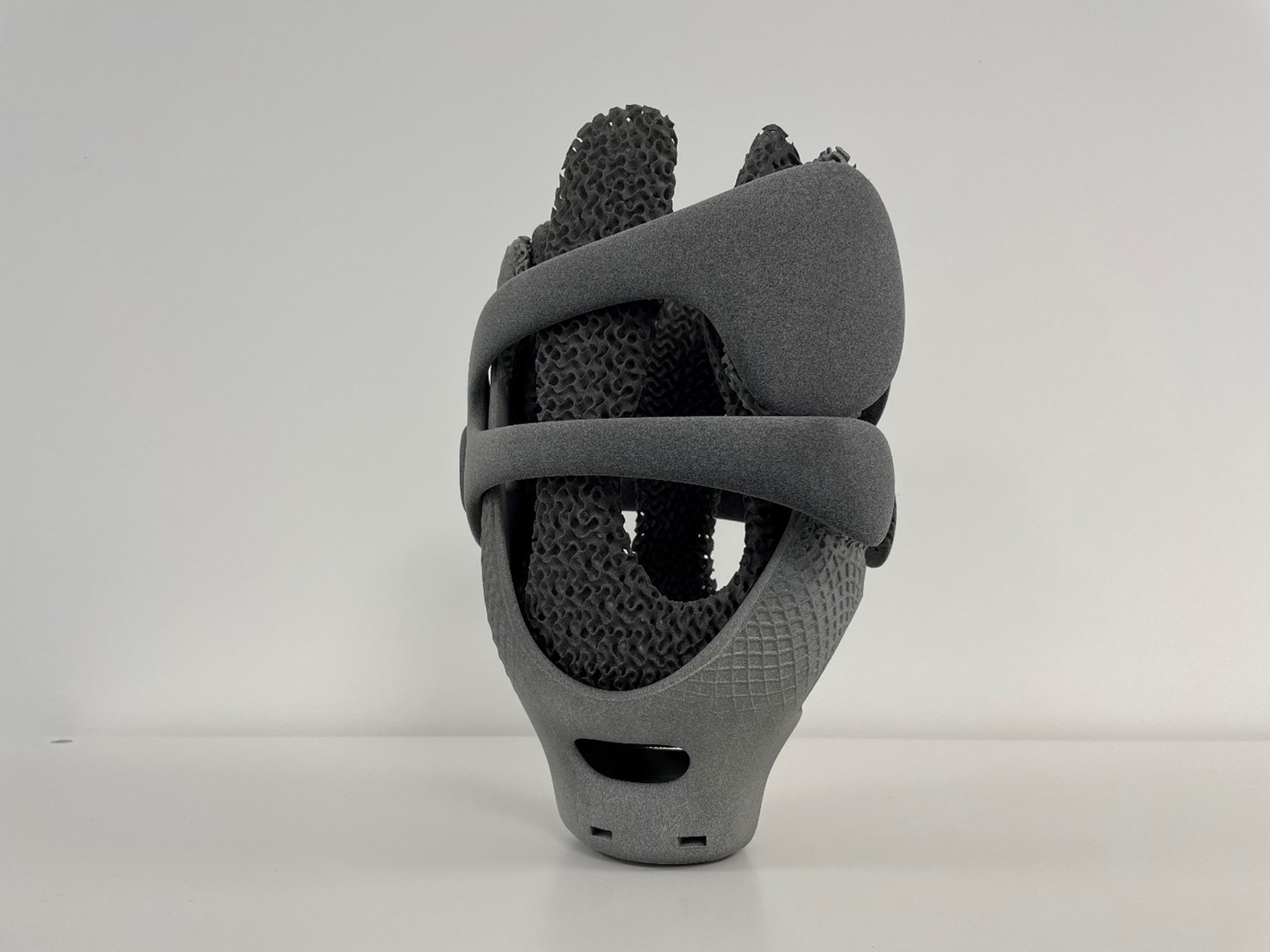
The project
The patient raised various problems, among which the following emerged: the need to have a breathable prosthesis that somehow allows air to pass through, a reduction in the weight of the structure to facilitate movements, greater comfort, therefore a more enveloping and “soft”, and finally a very high level of adaptability/personalization.
Development
The combination of additive technologies with specific design techniques led us to an extraordinary result.
We have in fact created a structure that maximizes the supply of air and, at the same time, minimizes direct contact with the leg in order to eliminate the thick silicone sock necessary for the vacuum. An architected material based on the gyroidal TPMS structure, therefore on mathematical formulas, guarantees more precise control over both compliance and variable thicknesses.
To reduce weight we started from an optimization and integration of shapes and structures, ensuring 5 fundamental points for support and containment. Additionally, we used directional ribs to stiffen the structure so we could maintain a lightweight yet sturdy design.
Starting from the consideration that the comfort of the prosthesis can vary over the course of weeks, months, years due to the evolution of the morphology of the stump, or even within the same day depending on the activity carried out, the use of the Gyroidal TPMS structure allowed for a more uniform distribution of loads and stresses.
The macro-shape resembles a flower with 5 petals, an association born from the analysis of the points of attachment and of greatest discomfort for the patient. An internal structure with controlled softness separated from the rigid external part was therefore created.
The integration between the adaptive comfort functionality and the cushioning function leaves the structure almost completely suspended in the central part of the base.
The soft inner lining provides an advanced grip capable of adapting the fit as the morphology of the limb fluctuates. Since the gyroidal structure is based on surfaces, we chose not only to re-map the geometry in a cylindrical way to accommodate conformity with the stump, but also to decrease the thickness with a double gradient from the inside (leg) to the outside (rigid prosthesis ), so as to work the central part or the part closest to the rigid part.
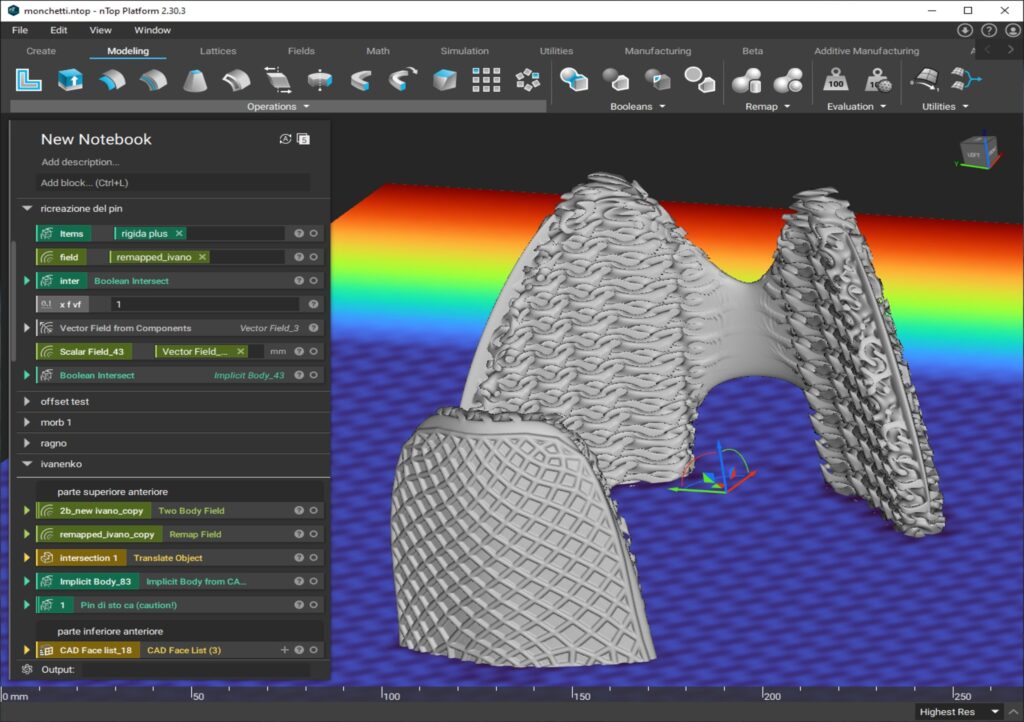
Form = Function
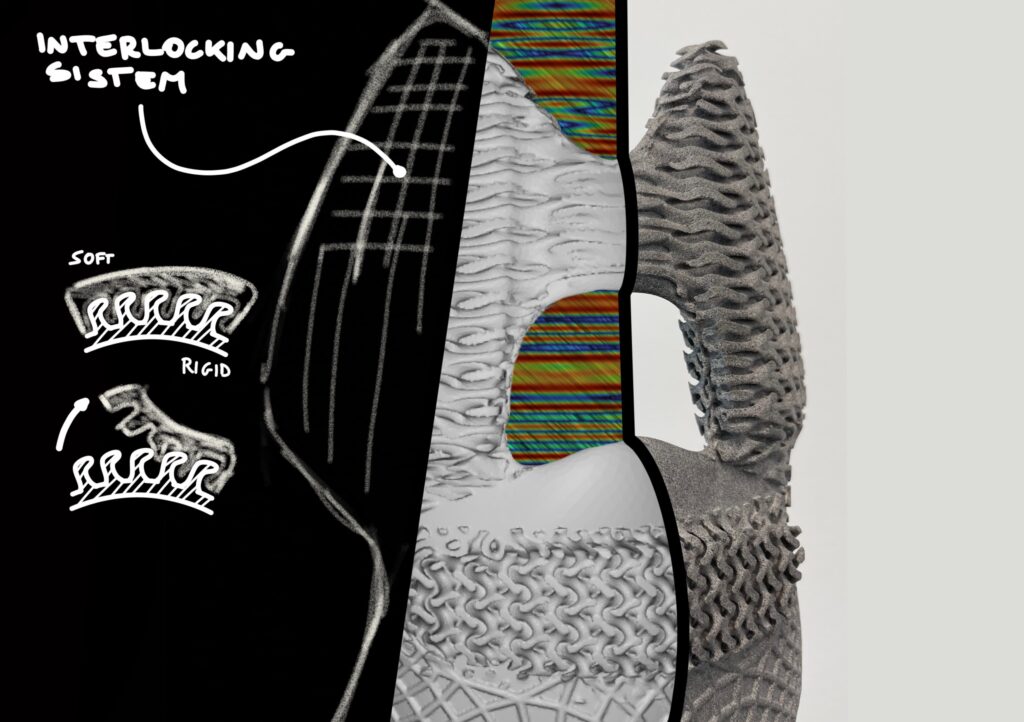
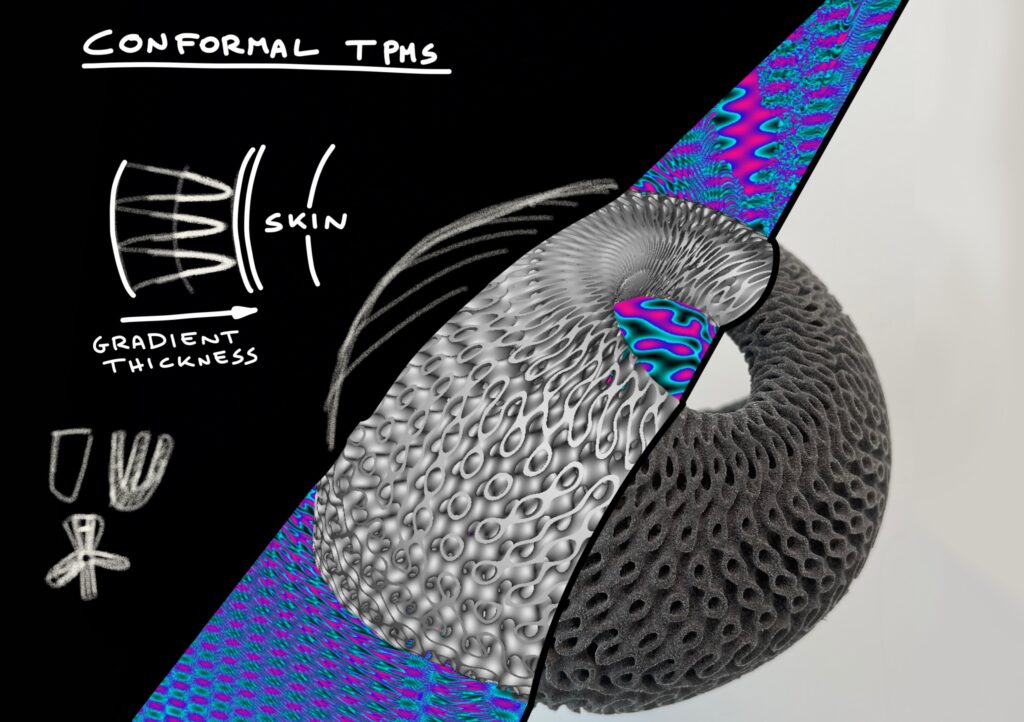
MJF HP technology perfectly matches all the needs of this project.
The PA12 material used for the external part gave the right balance between flexibility and rigidity of the component, while the TPU perfect for creating the soft part is also biocompatible, therefore ideal for contact with the skin.
We strongly believe that a specific combination of shape and materials, together with a specific suspension system, determines the good design for more comfortable and breathable dentures. During the development phases of our project, we took all these interconnected parameters into account and overcame the old labor-intensive and time-consuming mold design process with Additive Manufacturing..
The project in numbers
Time reduction
2/3 weeks
vs
1 week
Weight reduction
- 62%
Cost reduction
384€ cad
vs
88€ cad
Stress reduction
- 38%