Motorcycle frame
Topology Optimization
Our project focuses on the re-design of a motorcycle frame with an innovative design approach aimed at production using additive technologies. The main objectives include topological optimization to use material only where necessary, customization of the component to tailor it to the individual needs of riders, and reduction of time-to-market for new products. We started by scanning a frame created using traditional methods, and through successive iterations, we plan to develop a frame with optimal performance, manufactured using innovative technologies, and characterized by a unique design.
Project objectives
- Topological Optimization
- Customization
- Geometric Complexity
- Waste Reduction
- Reduction of Development Times
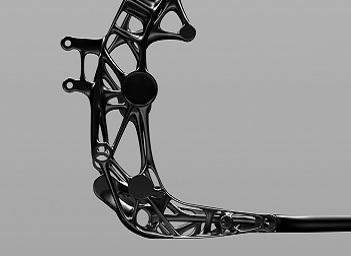
pROBLEM
The problem of the project was the need to redesign a motorcycle frame with the aim of fully exploiting the potential of additive manufacturing. Challenges include optimizing the structure, customizing the component for individual drivers and reducing the time to market for new products.
SOLUTION
The proposed solution is the creation of the frame using 3D printing and topology optimization. This approach allows the material to be used only where necessary, offering greater lightness and resistance. Furthermore, customizing the frame to adapt it to the needs of individual riders is possible thanks to the flexibility offered by 3D printing.
DEVELOPMENT
The project started with the scan of a frame made with traditional technologies. Subsequently, through iterations and the application of topology optimization, a new frame with optimal performance is expected to be developed. The use of 3D printing will allow the design to be quickly tested and adapted, speeding up the development process. The end result will be a lightweight, customized frame produced using innovative technologies and an exclusive design.
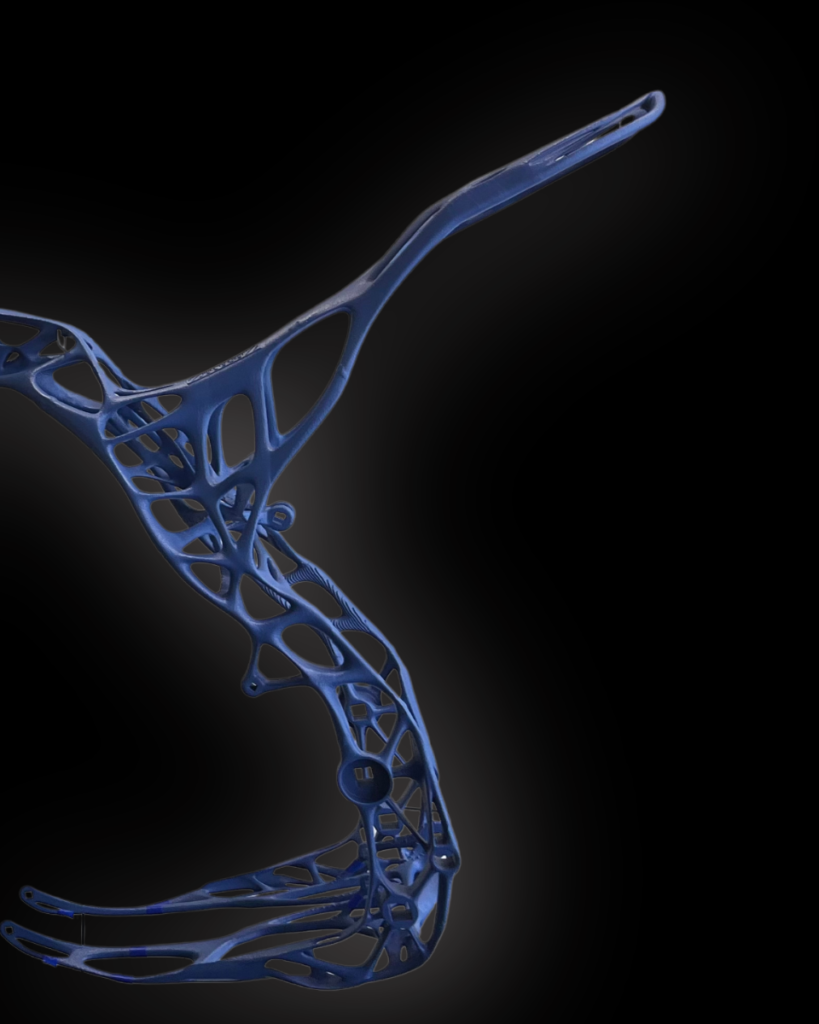
Intro
The traditional production of motorcycle frames presents some challenges, such as production complexity, design limitations, excessive weight, long production times, customization difficulties and generation of material waste. To address these issues, the adoption of 3D printing is being considered. This technology could enable more complex designs and structural optimizations, reduce production times, facilitate customization for pilots and minimize material waste. However, it is important to carefully evaluate the specific needs of the industry and ensure that 3D printing meets the safety and reliability standards required for motorcycle frames.
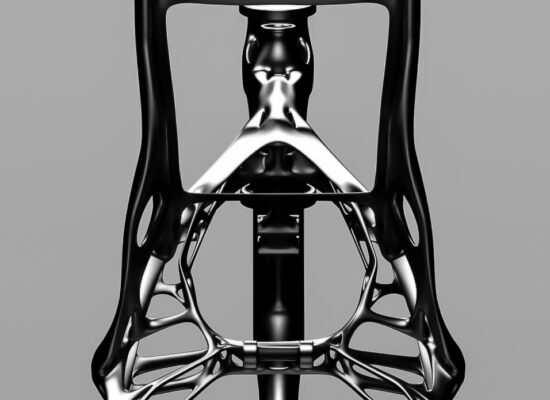
Immagine da progetto grabcad “cae-shifter-for-bmw
The project
3D printing has made significant progress in producing reliable structural components in industries such as aerospace, automotive and medicine. Some crucial factors to consider include choosing the right material, understanding mechanical properties, optimized design for additive manufacturing (DfAM), validating and certifying to standards, managing size and scalability for larger components, as well as the use of advanced manufacturing processes such as laser melting. Ultimately, additive manufacturing offers significant potential for producing efficient structural components, but it is essential to carefully evaluate the specific needs of the application and ensure compliance with safety standards and industry regulations.
Development
The creation of a frame using 3D printing goes beyond the optimized design in terms of shape and structure. Print optimization is an essential aspect to consider in the complete development of this project.
During the process of 3D printing a frame, several factors influence the quality and efficiency of the final result. First, you need to carefully weigh the need for supports for more complex or inclined structures. Correct handling of supports is crucial to ensure stability during printing and simplify subsequent removal, avoiding possible damage to the main structure.
Furthermore, removing residual dust, especially in intricate components, requires special attention. Limited access to certain areas can make this phase delicate, and the adoption of adequate tools and processes becomes crucial to obtaining a clean and residue-free surface.
Choosing the optimal machine filling is equally critical. Correct filling affects the solidity and resistance of the frame, avoiding excessive waste of material and improving the energy efficiency of the printing process.
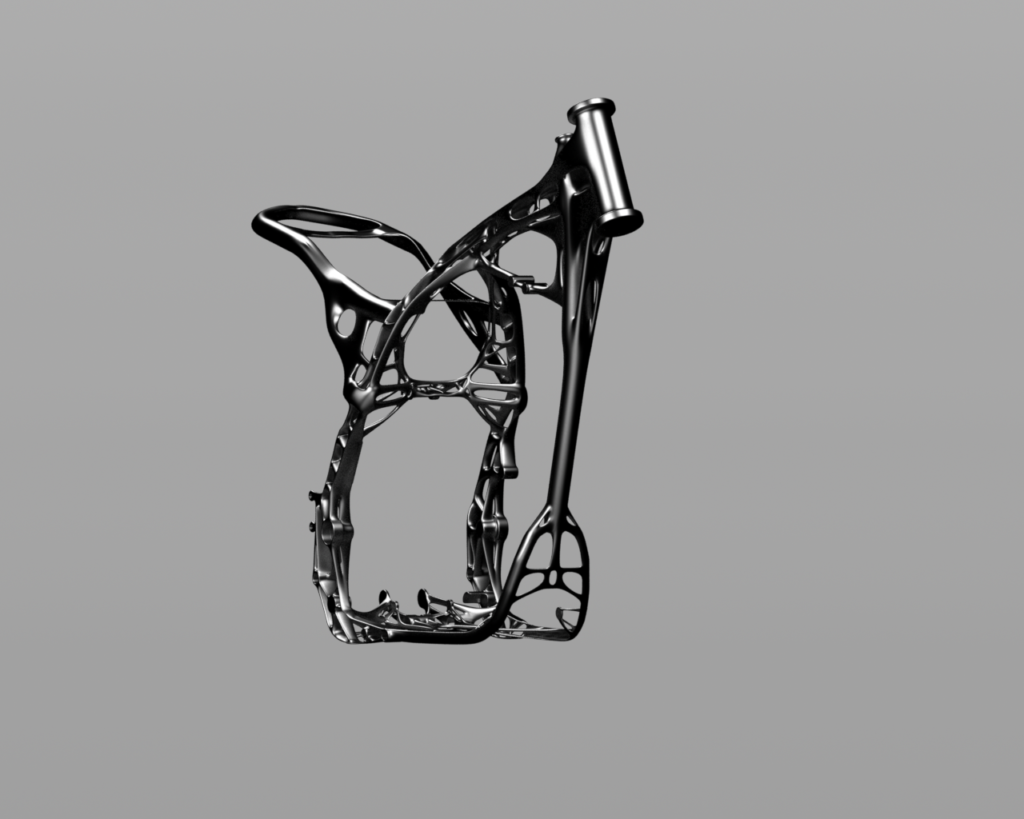
Print optimization is an integral and crucial part in the development of a 3D printed frame. Carefully considering aspects such as supports, dust removal and optimal machine filling ensures not only efficient production, but also a high-quality final product, meeting the specific challenges present in this advanced manufacturing methodology.
As a result, these complications lead to an expensive and slower process than AM and with lower performance results. Obviously the choice of a metallic material (we are talking about classic production) is necessary for the result you want to obtain but in the world of 3D printing you can think differently, there are also other paths.
Form = Function
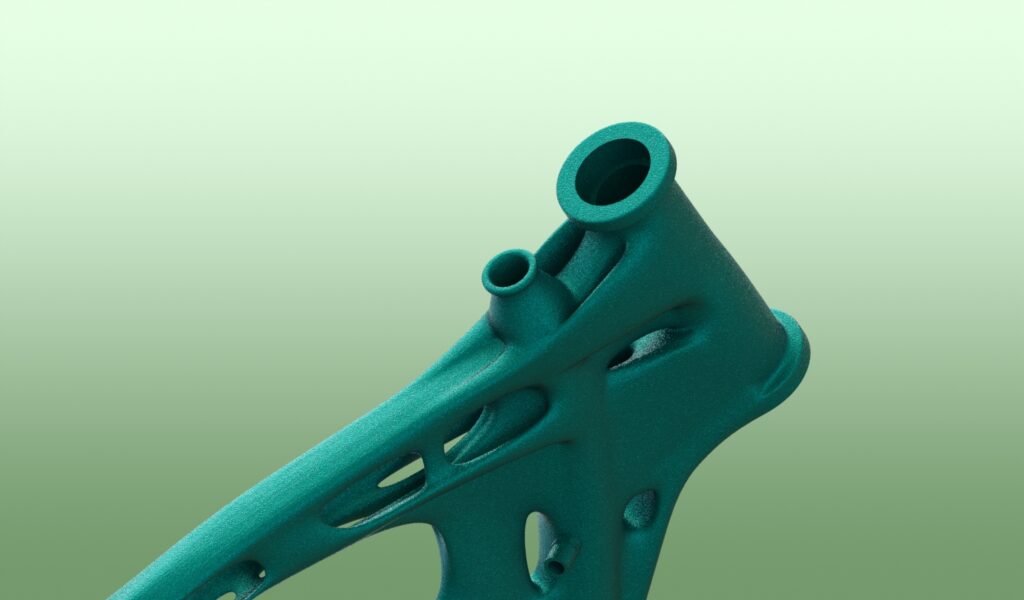
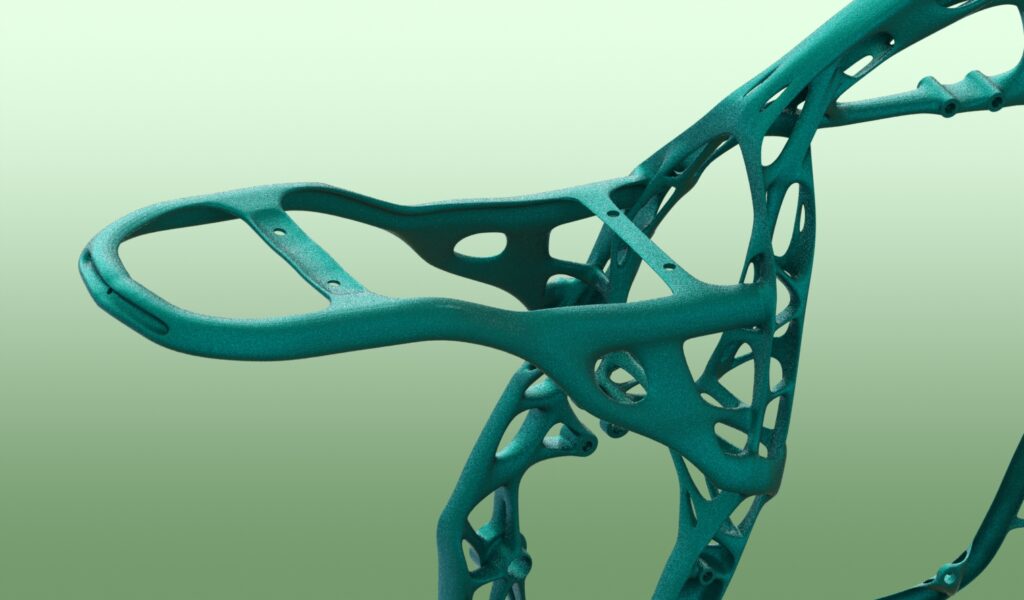
Object design should be guided by its main functions or purposes rather than by aesthetic or stylistic considerations. In other words, the shape of an object should derive directly from its functions and the practical needs it must satisfy.
In an engineering context, this principle implies that the design of a component, device or system should be optimized to maximize operational efficiency and functional performance. The shape of the object should be determined by specific usage needs, loading conditions, ease of production and other functional factors.
This approach promotes efficiency in design, reducing the superfluous and focusing attention on practical aspects. For example, when designing a chassis for a vehicle, the shape of the structure should be optimized to ensure maximum strength with as little weight as possible, taking into account the forces and strains that the object will experience during use.