Can technology improve our life quality?
Today the task of doctors, engineers and many other categories of professionals is to make our lives better, and this is exactly the main objective of this project: to make our engineering knowledge available to improve the life of those who, for example, every day has to wear a prosthesis to be able to carry out normal routine activities and more.
This project stems from a real case, from the needs of a patient who has not yet found the ideal prosthetic solution for his lifestyle.
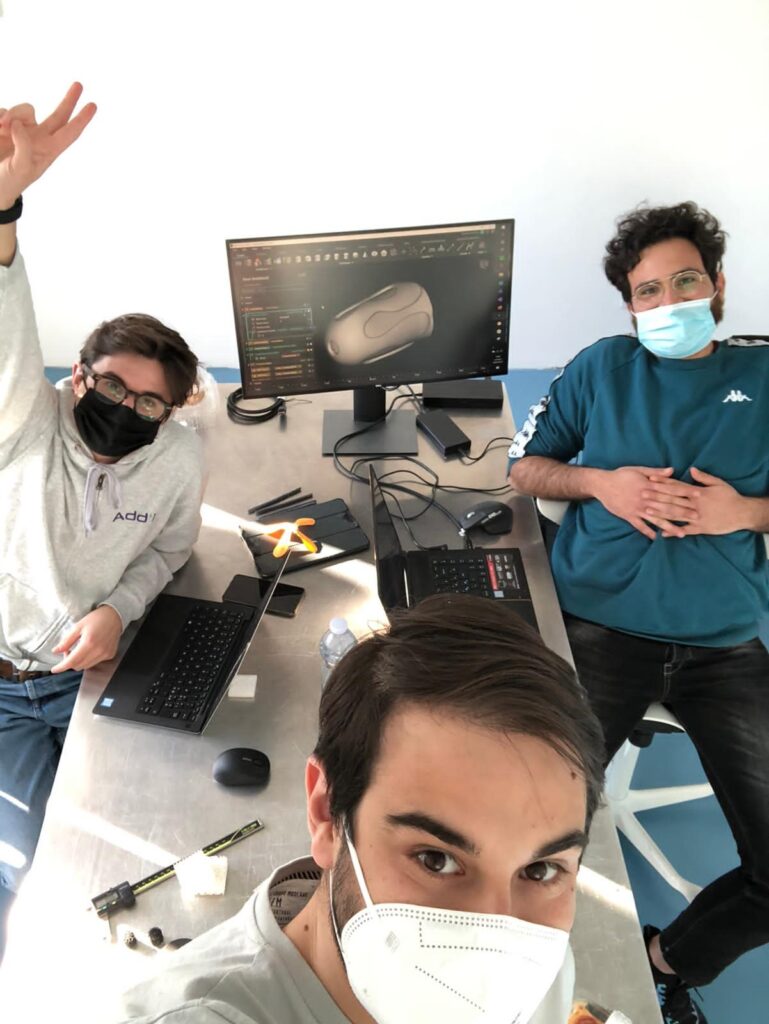
A working team of very young experts in Design for Additive Manufacturing – Francesco Leonardi and Ivan Vecchio (from PUNTOZERO’s team) and Gianluigi Rossi (from Additive Italia srl) – starting from the idea and analyzing the state of the art on prosthetics made by 3D printing, has designed an innovative solution:
sustainable, scalable and repeatable, but above all, that would satisfy the patient’s requests.
We strongly believe that a specific combination of shape and materials, together with a specific suspension system, determines the good design for more comfortable and breathable prostheses. During the development phases of our project, we considered all these interlinked parameters and we have passed the old style and time-consuming mould process thanks to Additive Manufacturing.
Cit. Francesco Leonardi
Breathability, lightening, comfort and adaptability
The patient highlighted several problems, among which emerged: the need to have a breathable prosthesis that somehow allows an air passage, a weight reduction on the structure to facilitate movements, greater comfort, and finally a very high level of customization.
The combination of additive manufacturing technologies with specific design techniques led us to an extraordinary result.
We created a structure that maximizes the supply of air and, at the same time, minimizes the direct contact with the leg in order to eliminate the thick silicone sock necessary for vacuum packing.
An architected material based on the gyroidal TPMS structure, therefore on mathematical formulas, guarantees more precise control both on compliance and on variable thicknesses.
To reduce the weight, we started with an optimization and integration of shapes and structures, ensuring 5 fundamental points for support and containment. In addition, we used directional ribs to stiffen the structure in this way we have been able to keep a light but strong design.
Starting from the consideration that the comfort of the prosthesis can vary over a period of weeks, months, years depending on the evolution of the morphology of the stump, or even within the same day depending on the activity performed, the use of the gyroidal TPMS structure allowed a more uniform distribution of loads and stresses.
The macro-shape resembles a flower with 5 petals, an association born from the analysis of the attachment points and of greatest discomfort for the patient.
Was therefore created an internal structure with controlled softness, separated from the rigid external part.
The integration between the adaptive comfort function and the cushioning function leaves the structure almost completely suspended in the central part of the base.
The soft inner lining constitutes an advanced grip able to adapt the fit according to the fluctuation of the morphology of the limb. Since the gyroidal structure is based on surfaces we have chosen not only to re-map the geometry in a cylindrical way to accommodate compliance with the stump, but also to decrease the thickness with a double gradient from the inside (leg) to the outside (rigid prosthesis), to stress the central part or the one closest to the rigid.
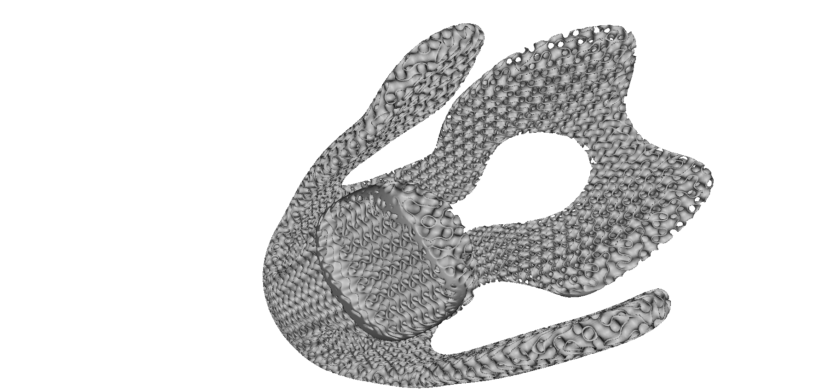
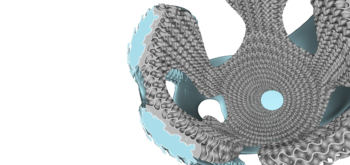
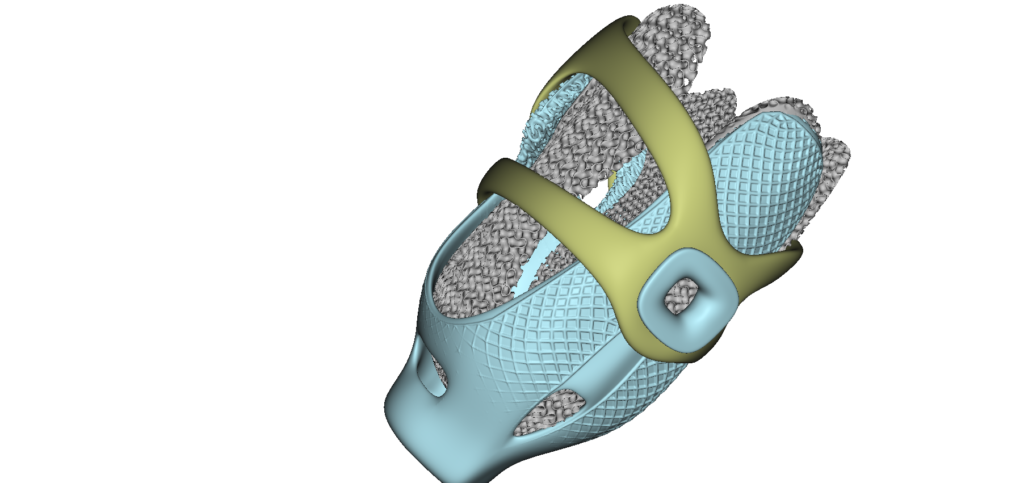
The soft internal structure has been separated from the rigid in order to have a quick removal and interchange between different internal padding optimized for different activities or for an evolution in healing and therefore in the morphology of the stump.
Thinking additive was the key to the success of this project.
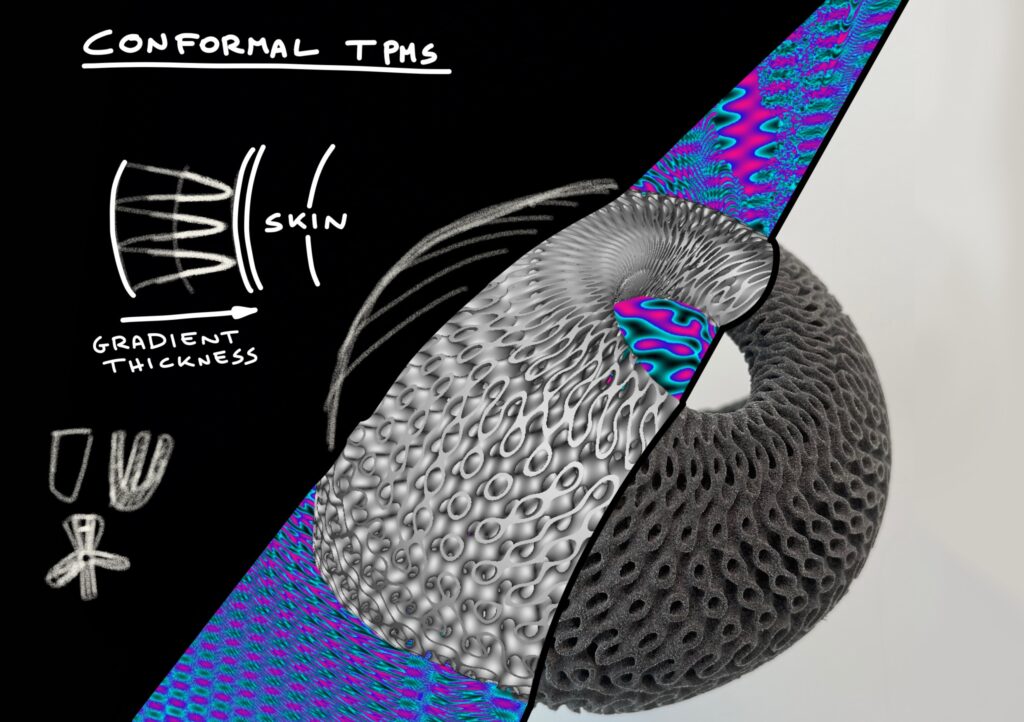
MJF HP MJF HP guarantees: sustainability, scalability and repeatability
HP MJF technology perfectly matches all the needs of this project.
The PA12 material used for the external part has given the right balance between flexibility and stiffness of the component, while the TPU, perfect for creating the soft part, is also biocompatible, therefore ideal for skin contact.
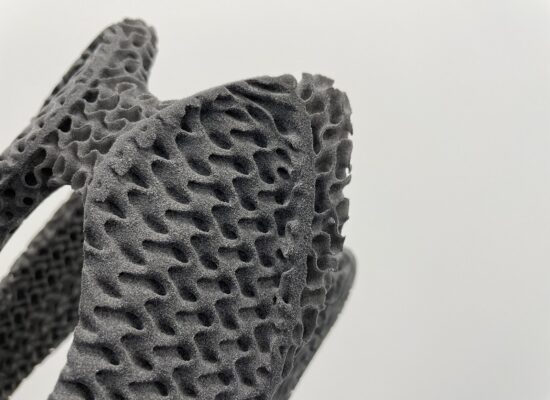
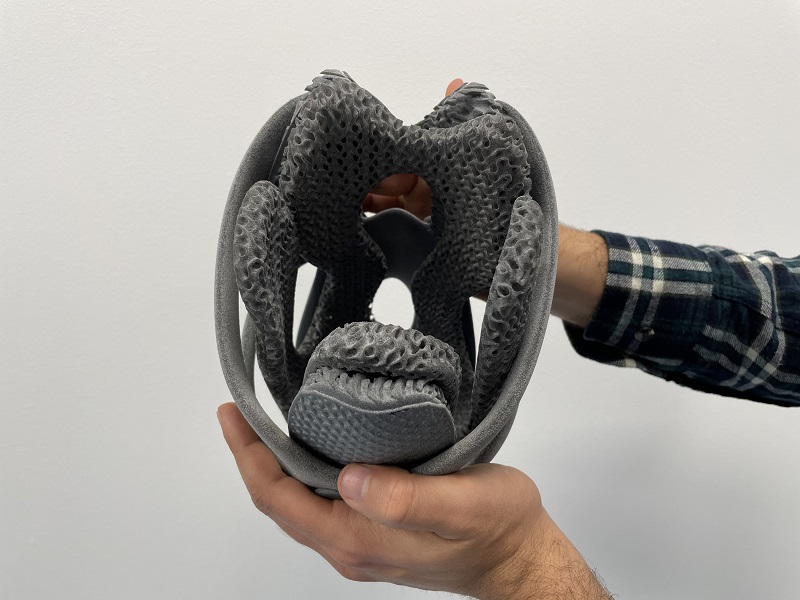
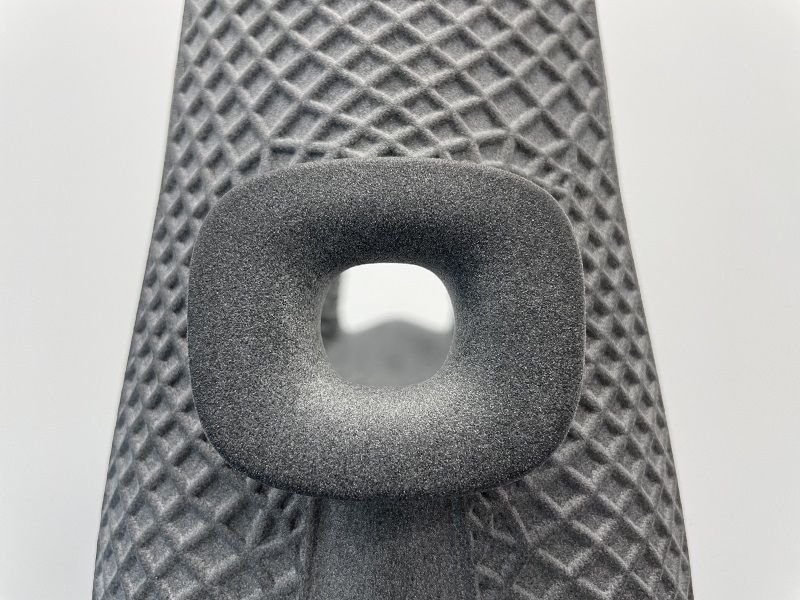
As we said, the main objective of the project is to solve all the problems highlighted by the patient. The secondary goal that we set ourselves was to develop a solid but at the same time dynamic process, to be applied to other patients and to have the possibility to modify the parameters for a complete customization, for a quick adaptation to the morphology evolution and for a constant improvement of the product, guided not only by numerical inputs but by direct user feedback.
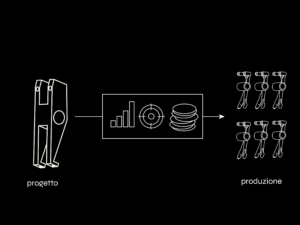
The use of AM technology also allows us to think of a flexible, rapid and relatively cheap production process.
Starting from natural inspiration helps us to engineer our products in an optimal way, as in most of the projects we deal with. The natural shape of this component arises from the need to integrate and “grow” parts with different functions within a single component.
The most significant example of this aspect is the integrated interlocking mechanism inspired by a Velcro™.
We arrived at this solution following numerous iterations and a series of steps of mathematical functions created using nTopology software.
The advantages derive both from the design and the process used, and the combination of the two allows us to exploit many typical AM opportunities and transform them into concrete solutions.
Designing a product knowing that you can rely on the potential of additive technologies, allows you to take advantage of innovative materials and geometries, engineered to go beyond the limits of traditional techniques.
PUNTOZERO
Design for Additive Manufacturing
Contact
- info@puntozero3d.com